Cold weather often poses threats to commercial buildings, as the constant cycle of freezing and thawing can relentlessly attack structural integrity.
This relentless expansion and contraction of water within building materials can lead to microscopic cracks that gradually widen, compromising critical moisture barriers over time.
You can get a strong emphasis on building durability and infrastructure development worldwide through the global waterproofing market. Initially, it was valued at USD 35.83 billion in 2024 and is projected to grow to USD 45.50 billion by 2030 [Source: GlobalNewswire].
But by understanding every key aspect, you can safeguard your commercial property against the harsh realities of winter. Let’s learn everything in this article, from key waterproofing considerations to commercial waterproofing services.
KEY TAKEAWAYS
- Repeated freezing and thawing of moisture gradually widens cracks in building materials, compromising waterproofing.
- Use flexible, cold-tolerant materials like modified bitumen, hot fluid-applied systems, and synthetic membranes.
- Implement under-slab barriers, bentonite clay, and proper drainage to protect foundations from subsurface moisture.
- Apply durable, traffic-grade coatings and consider heated elements or sloped designs for roofs and decks to manage snow and ice.
- Experienced contractors select specific cold-weather systems and adjust application methods for year-round protection.
Understanding How Freeze-Thaw Cycles Affect Materials
Water seeps into cracks and later escapes as it melts when temperatures hover near freezing. This expansion results in the gradual widening of gaps in stone, concrete, and protective coatings. Eventually, these openings increase, they can allow more water to pass through, which gives rise to more severe issues over time.
Flexible and cold-tolerant waterproofing materials are usually determined to minimize these effects. Thermoplastic membranes and rubberized systems are built to expand and contract moderately as temperatures change over time. This allows for maintaining the connection between layers and reduces the possibility of premature failure.
Selecting the Right Materials for Cold Weather Use
Not every waterproofing item reacts equally to cold temperatures in the same way. Certain coatings and adhesives may become brittle or lose their ability to bond effectively in freezing conditions, which might cause premature deterioration after application. This emphasizes how crucial it is to select materials precisely suited for colder climates.
The following are commonly used choices that function well in low temperatures:
- Modified bitumen: Offers flexibility and longevity in freezing conditions.
- Hot fluid-applied systems: Form perennial barriers that are kept stable through cycles of expansion and contraction induced by temperature changes.
- Synthetic membranes: Withstand cracking and maintain waterproof behavior even in freezing temperatures.
Contractors might also depend on cold-weather primers and flexible application timing to promote superior adhesion and performance.
Focusing on Protection Below Ground Level
When snow melts or heavy rain soaks the soil, subsurface moisture can lead to problems. Water may try to sneak inside a building by exerting pressure on its foundation. Over time, if this is left unchecked, it impacts the foundation.
Contractors use bentonite clay systems, under-slab barriers, and fluid coatings to protect the lower portions of buildings. Suitable drainage management systems also direct water away from the foundation. When these techniques are used together, they help reduce the possibility that moisture may seep into interior walls.
INTERESTING FACT
“Water damage is a leading cause of property insurance claims, accounting for nearly 23.8% of all homeowner claims in the US in 2022, second only to wind and hail.”
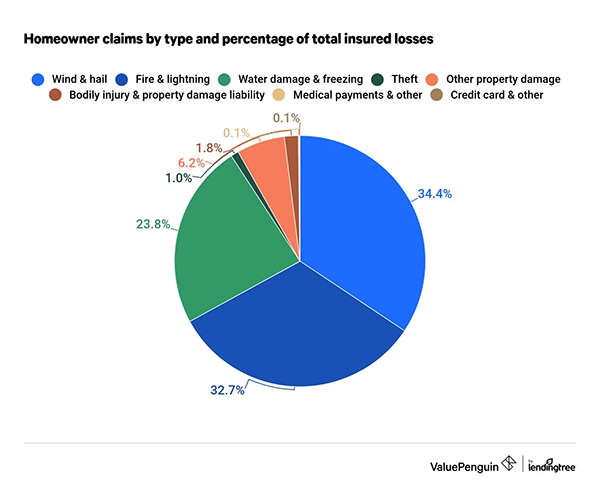
Handling Snow Load and Ice on Exposed Surfaces
Parking decks, roofs, and walkways experience intense snow buildup and crusty ice in cold areas. When melted water gets trapped under surface coatings and refreezes, it can lift or crack the top layer. This puts pressure on every aspect of the structure and the materials protecting it.
To prevent this, planners select traffic-grade coatings that are cold-weather durable. These surfaces are capable of withstanding weight and resisting movement caused by temperature fluctuations. In certain instances, buildings employ heated drains or sloped designs to promote water runoff and minimize accumulation.
Solutions Commonly Used by Building Professionals
Professionals assigned to work on large-scale moisture protection projects usually choose from a wide range of cold-weather systems. These might include spray-applied waterproofing, hot-applied rubberized layers, and high-performance membranes that are suited for foundations, roofs, and decks.
Experienced contractors ensure the structure stays protected year-round by evaluating the site conditions and selecting appropriate methods. Some companies also modify installation schedules and material handling based on seasonal scenarios to improve durability and performance.
Commercial waterproofing services have become a key component of building planning in cold-weather regions. They provide the systems and knowledge required to protect below-ground spaces, manage freeze-thaw cycles, and manage snow and ice exposure. With the desirable materials and proper application, buildings are better enabled to withstand the demands of winter without serious damage. Early planning and thoughtful mechanism choices help reduce risks and improve structural resilience.
How do freeze-thaw cycles damage buildings?
Water seeps into cracks, freezes, and expands, widening the gaps. When it thaws, more water can enter, leading to damage to materials and structures over time.
What types of waterproofing materials are best for cold climates?
Materials that remain flexible and durable in low temperatures, such as modified bitumen, hot fluid-applied systems, and synthetic membranes, are ideal.
Why is below-ground waterproofing important in cold weather?
Melting snow and rain can create hydrostatic pressure against foundations. Proper below-ground barriers prevent this moisture from seeping into interior walls and damaging the foundation.
How do buildings protect against snow and ice buildup on roofs and decks?
Using traffic-grade, cold-weather durable coatings, heated drains, or sloped designs helps manage snow load, prevent ice formation, and ensure proper water runoff.